Cold Mix Recycling
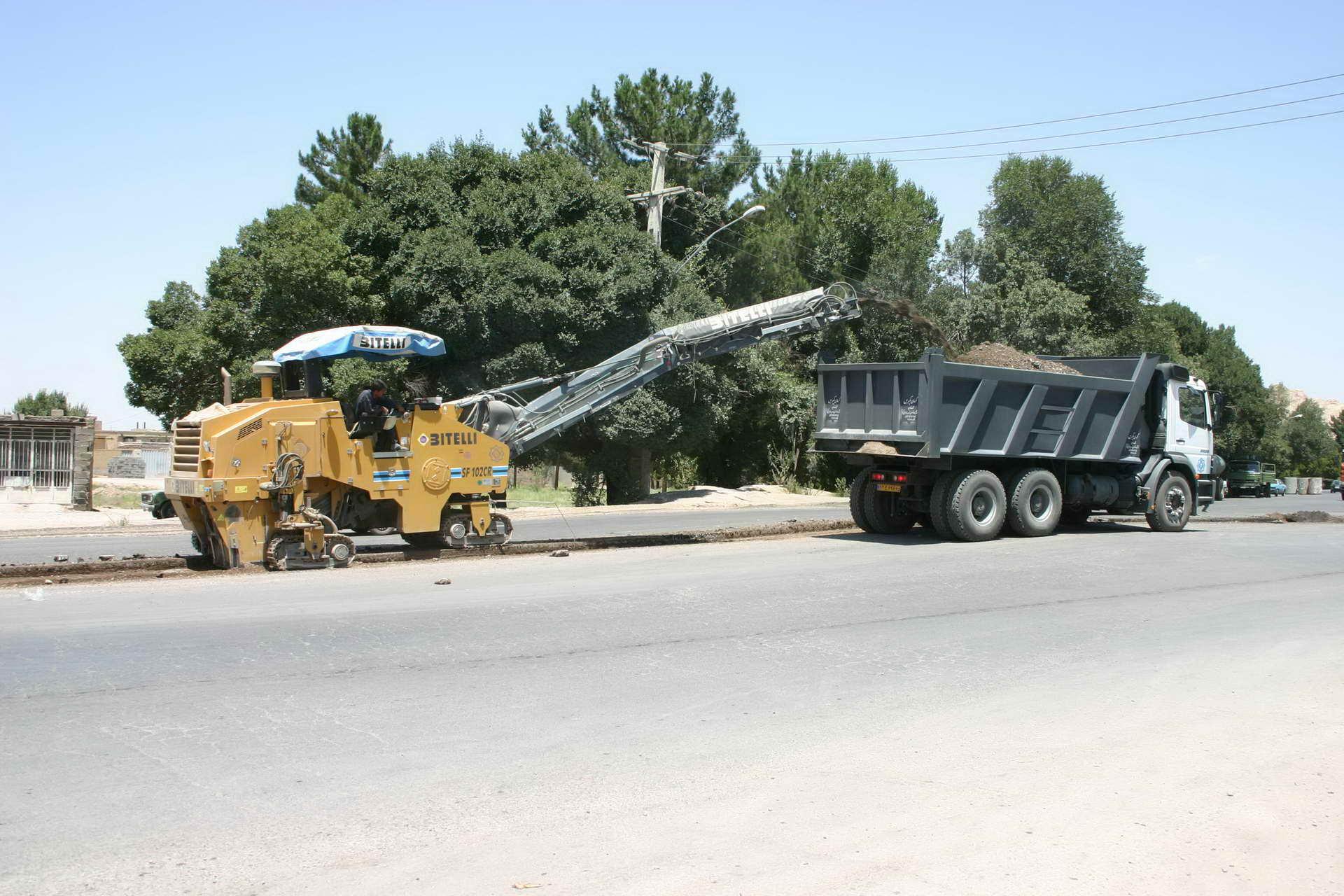
Recycling is typically carried out as a means of treating distressed pavement structures with granular bases and relatively thin surfacing that are normally comprised of either asphalt or multiple seals. Distress in such pavements is usually manifest in the form of severely cracked asphalt layers, deformed granular layers and potholing. Thepurpose of adding stabilizing agents whilst recycling is to restore structural integrity by improving the engineering properties of the recovered materials whilst simultaneously achieving the required riding quality.
Recycling of the exiRecycling is typically carried out as a means of treating distressed pavement structures with granular bases and relatively thin surfacing that are normally comprised of either asphalt or multiple seals. Distress in such pavements is usually manifest in the form of severely cracked asphalt layers, deformed granular layers and potholing. The purpose of adding stabilizing agents whilst recycling is to restore structural integrity by improving the engineering properties of the recovered materials whilst simultaneously achieving the required riding quality. Recycling of the existing gravel wearing course is usually carried out in conjunction with the addition of stabilizing agents. Stabilizing with either bitumen emulsion or foamed bitumen is normally carried out to a recycled depth of between 125 mm and 150 mm with a thin surfacing, such as a chip seal or slurry seal. Stabilizing with either cement or hydrated lime requires the depth of recycling to be increased to between 150 mm and 250 mm to achieve a similar product in terms of structural life, but not durability. An additional application that falls into this category is the modification of plastic material by recycling with hydrated lime. During the recycling process, only sufficient lime is added to modify (eliminate) plasticity and is therefore not considered as stabilization since the reason for adding the lime is not to be achieve strength gain (although in the long term, some increase in strength may result). Cold recycling can be achieved either in-plant by hauling material recovered from an existing road to a central depot where it is fed though a processing unit, or in-place using a recycling machine. In-place treatment is popular due to the advent of large powerful recycling machines that can rehabilitate pavements at a fraction of the cost of conventional reconstruction methods. And, in light of pavement deterioration worldwide, rehabilitation of existing pavements far exceeds the demand for new roads.. Benefits of Cold Recycling: 1. Environmental factors. Full use is made of the material in the existing pavement. Spoil sites do not have to be found and the volume of new material that has to be imported from quarries is minimized. This reduces scars in the countryside that are inevitable when opening quarries and borrow pits. Haulage is drastically reduced. The overall energy consumption is thus significantly reduced, as is the damaging effect of haulage vehicles on the road network. 1. 2. Quality of the recycled layer. Consistent, high quality mixing of the in-situ materials with water and stabilizing agents is achieved. The addition of fluids is accurate due to micro-processor controlled pumping systems. The recycled material and additives are rigorously mixed together in the mixing chamber. 3. Structural integrity. The cold recycling process produces thick bound layers that are homogeneous and do not contain weak interfaces between thinner pavement layers. 4. 4. Sub-grade disturbance is minimized. Disturbance of the underlying pavement structure is minimal compared to pavement rehabilitation using conventional construction equipment. Cold recycling is typically a single-pass operation. When using a track-mounted recycler, the rear tracks pass only once on the exposed underlying material Tire-mounted recyclers spread the material behind the machine avoiding any contact between the tires and the exposed underlying pavement structure. (Reworking pavement material with conventional construction equipment often results in the sub-grade being subjected to repeated high stress loading, causing heaving conditions that have to be excavated and backfilled with fresh imported material). 5. Shorter construction time. Recyclers are capable of high production rates that significantly reduce construction times compared to alternative rehabilitation methods. Shorter construction times reduce project costs as well as providing a largely intangible benefit for the road user in the reduced time that traffic is disrupted. 6. 6. Safety. One of the most important benefits of this process is the high level of traffic safety that can be achieved. The full recycling train can be accommodated within the width of one traffic lane. For example, on roads with two traffic lanes, recycling can be carried out along one half of the road -width during the day and the full-road width, including the completed recycled lane, can be opened to traffic by nightfall. 7. Cost effectiveness. The above benefits all combine to make cold recycling a most attractive process for pavement rehabilitation in terms of cost effectiveness.sting gravel wearing course is usually carried out in conjunction with the addition of stabilizing agents. Stabilizing with either bitumen emulsion or foamed bitumen is normally carried out to a recycled depth of between 125 mm and 150 mm with a thin surfacing, such as a chip seal or slurry seal. Stabilizing with either cement or hydrated lime requires the depth of recycling to be increased to between 150 mm and 250 mm to achieve a similar product in terms of structural life, but not durability. An additional application that falls into this category is the modification of plastic material by recycling with hydrated lime. During the recycling process, only sufficient lime is added to modify (eliminate) plasticity and is therefore not considered as stabilization since the reason for adding the lime is not to be achieve strength gain (although in the long term, some increase in strength may result). Cold recycling can be achieved either in-plant by hauling material recovered from an existing road to a central depot where it is fed though a processing unit, or in-place using a recycling machine.
In-place treatment is popular due to the advent of large powerful recycling machines that can rehabilitate pavements at a fraction of the cost of conventional reconstruction methods. And, in light of pavement deterioration worldwide, rehabilitation of existing pavements far exceeds the demand for new roads.. Benefits of Cold Recycling:
1. Environmental factors. Full use is made of the material in the existing pavement. Spoil sites do not have to be found and the volume of new material that has to be imported from quarries is minimized. This reduces scars in the countryside that are inevitable when opening quarries and borrow pits. Haulage is drastically reduced. The overall energy consumption is thus significantly reduced, as is the damaging effect of haulage vehicles on the road network.
1.
2. Quality of the recycled layer. Consistent, high quality mixing of the in-situ materials with water and stabilizing agents is achieved. The addition of fluids is accurate due to micro-processor controlled pumping systems. The recycled material and additives are rigorously mixed together in the mixing chamber.
3. Structural integrity. The cold recycling process produces thick bound layers that are homogeneous and do not contain weak interfaces between thinner pavement layers.
4. 4. Sub-grade disturbance is minimized. Disturbance of the underlying pavement structure is minimal compared to pavement rehabilitation using conventional construction equipment. Cold recycling is typically a single-pass operation. When using a track-mounted recycler, the rear tracks pass only once on the exposed underlying material Tire-mounted recyclers spread the material behind the machine avoiding any contact between the tires and the exposed underlying pavement structure. (Reworking pavement material with conventional construction equipment often results in the sub-grade being subjected to repeated high stress loading, causing heaving conditions that have to be excavated and backfilled with fresh imported material).
5. Shorter construction time. Recyclers are capable of high production rates that significantly reduce construction times compared to alternative rehabilitation methods. Shorter construction times reduce project costs as well as providing a largely intangible benefit for the road user in the reduced time that traffic is disrupted.
6. 6. Safety. One of the most important benefits of this process is the high level of traffic safety that can be achieved. The full recycling train can be accommodated within the width of one traffic lane. For example, on roads with two traffic lanes, recycling can be carried out along one half of the road -width during the day and the full-road width, including the completed recycled lane, can be opened to traffic by nightfall.
7. Cost effectiveness. The above benefits all combine to make cold recycling a most attractive process for pavement rehabilitation in terms of cost effectiveness.